With more than an estimated 54,000 storage units spread across the U.S. in 2015, according to IBISWorld, and 2.63 billion square feet of existing rentable self-storage space in 2014, the self-storage industry is booming. In fact, U.S. storage facility revenue topped off at an estimated $29.8 billion in 2014, rising to $31 billion in 2015 and is expected to reach $32.7 billion in 2016. In this growing market, storage builders and facility owners face increased competition and must build and maintain more efficiently and effectively than ever. Metal panels can be a differentiator for this market, especially through multi-story and climate controlled storage facilities.
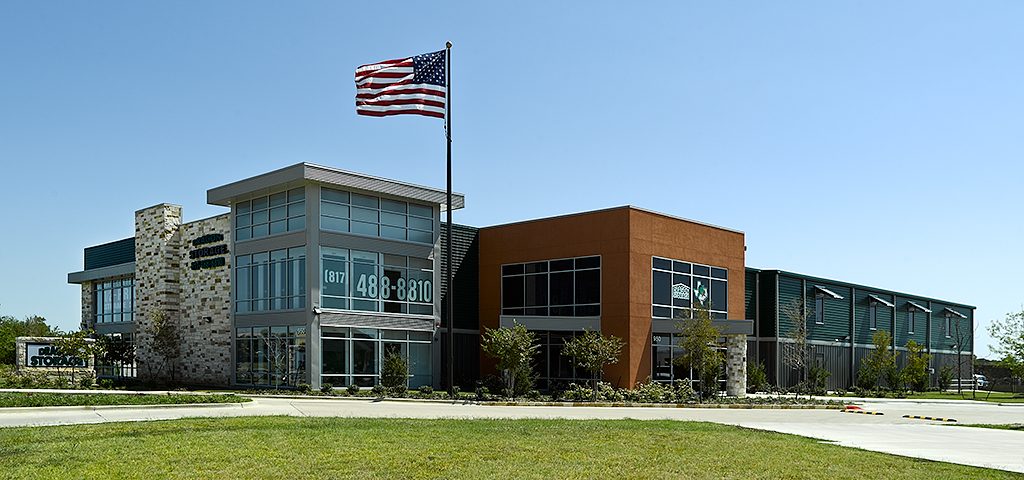
Maximizing Sustainable, Rentable Space
Among the cladding and roofing materials available to build these specialized facilities, insulated metal panels (IMPs) are highly energy efficient, deliver a full weather barrier and can be designed without exterior wall framing. This boosts rentable square footage by eliminating exterior wall framing typically built with studs, batt insulation, and liner panels.
Made from 90 percent closed foam, encapsulated inside of two metal panels and impervious to water, IMPs offer a high R-value, which is a big benefit for all storage types, particularly cold storage facilities. Steel panel facings create a vapor barrier and provide long-term thermal stability, virtually eliminating off-gassing found with rigid board insulation. IMPs give design professionals the opportunity to design functional, attractive, sustainable storage facilities, and facility owners the opportunity to lower construction, operating, energy consumption, and maintenance costs throughout the life span of a building.
As an all-in-one air solution—delivering an air, vapor and water barrier with continuous insulation—building teams can strip down the multiple trades to one single application. This means there are no gaps or voids to sap thermal value, and no degradation by air or moisture. Furthermore, IMPs are the most efficient product available, providing an R-value of 7 to 8 per inch vs. the 4.5 for batt insulation, essentially doubling performance. So not only do building teams come away with a thermally superior product, but the IMP storage facility will meet increasing continuous insulation code requirements, such as those mandated by ASHRAE 90.1.
Of course, increasing rentable square footage is one of the biggest draws about IMPs for building owners as those extra four to six inches on the perimeter go straight to the bottom line.
A Modern Style for Storage
Evolving from the standard-looking, plain boxes, today’s storage facilities are taking on a more architectural look to better blend into the office complexes, residential communities and retail complexes surrounding them.
With a variety of high-performance coatings, colors, reveal joints and corrugated sheets with assorted patterns, IMPs offer a large selection of design options to architects looking to create these more trendy designs.
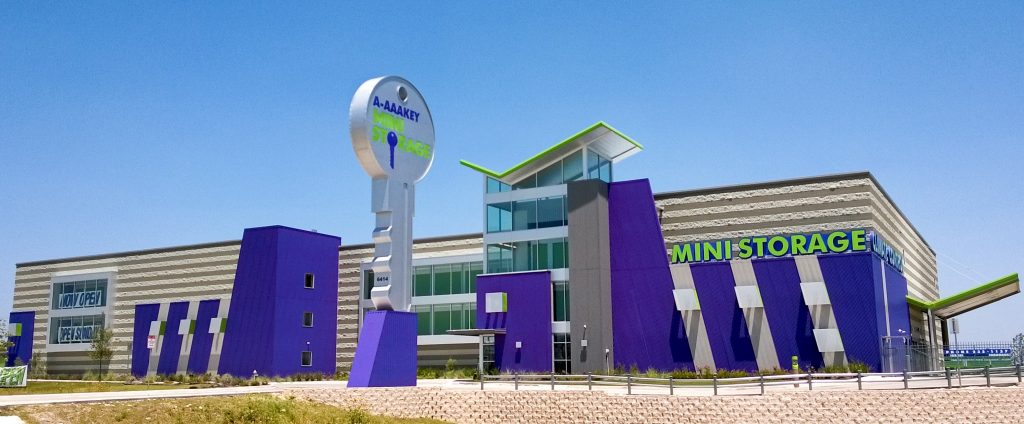
“The calculated use of smooth, concealed-fastener panels harkens to contemporary design styles with an eye toward the future,” states Ryan Rogers, managing partner, RHW Capital Management Group, Orange, Calif., in an Aug. 2016 issue of Inside Self-Storage. “This can create the perception of innovation and dynamism, communicating to customers that your facility is on the cutting edge of the industry and, as such, a successful leader.”
In order to capitalize on the design and performance options leveraged by IMP panels, architects are advised to integrate these systems from the project’s onset in order to maximize efficiencies and potentially take advantage of longer stands, greater distances and heavier steel gauges.
Multi-Level Storage Facilities
Moving forward, designers can expect to see an increase in multi-story storage facilities, particularly in urban areas, where building owners are being forced onto smaller lots.
Explaining the trend in a Sept. 2016 issue of Commercial Investment Real Estate magazine, Michael Haugh, CCIM, senior director of revenue management, Storage USA, Memphis, states, “Increased land costs have forced developers to build up, particularly in urban markets where land tracks of four or more acres necessary for single-story developments are nonexistent. In some cases, a multistory project can be built on as little as 1.5 acres.”
Or in regions where there is little space for new construction but a high demand for storage, like New York City, storage companies are renovating upward. For example, Stop & Stor partners with door and storage solution company, DBCI to convert existing buildings into high-end, multi-level storage facilities. Using existing building blueprints and outline unit placement, DBCI created a custom storage solution in a space that is both conveniently located and functional For more information, read “Urban Storage Units” in Metal Architecture’s Jan. 2016 issue.
Filling the Storage Niche
From multiple stories to designer-end architecture, IMPs are actively filling an important niche in the self-storage industry as a durable and aesthetic, all-in-one building enclosure solution.