In a prior post, we discussed the importance of independent (i.e. third party) standardized testing as a means of verifying the performance of metal roofing, and specifically looked at structural and wind uplift performance. In this post, we will similarly look at testing standards but focus on metal roofing tested for air leakage and water penetration.
Air Leakage and ASTM E1680
Keeping air from passing through a building system from the exterior to the interior (i.e. drafts) is a fundamental role of any building envelope system, including roofing. It is also important in controlling the flow of harmful airborne moisture into a roof assembly. Hence, testing a roofing panel for its ability to control air leakage is critical to the long-term success of the roofing system, and ultimately, the building.
ASTM E1680 “Standard Test Method for Rate of Air Leakage Through Exterior Metal Roof Panel Systems” is used to determine “the resistance of exterior metal roof panel systems to air infiltration resulting from either positive or negative air pressure differences”. It is a standard procedure for “determining air leakage characteristics under specified air pressure differences”. The test is applicable to the field portion of any roof area including panel side laps and structural connections but not at openings, the roof perimeter, or any other details. The test is also based on constant temperature and humidity conditions across the roofing specimen being tested to eliminate any variation due to those influences.
The standard test procedure consists of “sealing and fixing a test specimen into or against one face of an air chamber, supplying air to or exhausting air from the chamber at the rate required to maintain the specified test pressure difference across the specimen, and measuring the resultant air flow through the specimen”. Basically, the test is meant to reveal the ability of the selected roofing panel to resist the difference in air pressure between the two sides and thus demonstrate its air tightness.
The beauty of this standardized test is that different metal roofing products can be tested under the same conditions and compared. The standard calls for a pressure differential between the two sides of positive and negative 1.57 foot pounds of pressure per square foot of panel (75 paschals of pressure) and can be tested in the negative pressure mode alone if the roof slope is less than 30 degrees from horizontal.
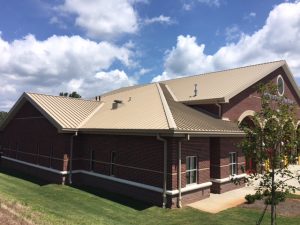
Water Penetration and ASTM E1646
In addition to air leakage, water leakage in roofing systems is obviously not desired. To test the performance of metal roofing products in this regard, ASTM E1646 titled “Standard Test Method for Water Penetration of Exterior Metal Roof Panel Systems by Uniform Static Air Pressure Difference” is the norm. This standard laboratory test is not based solely on free running water, but on water “applied to the outdoor face simultaneously with a static air pressure at the outdoor face higher than the pressure at the indoor face, that is, positive pressure”. This pressurized testing is intended to simulate wind-driven rain and flowing water that can build a head as it drains. The test measures the water-resisting properties of the roofing in the field of the roof panels including panel side laps and structural connections. Just like air testing, it does not include leakage at openings, perimeters, or other roofing detail areas.
The test method itself consists of “sealing and fixing the test specimen into or against one face of a test chamber, supplying air to or exhausting air from the chamber at the rate required to maintain the test pressure difference across the specimen, while spraying water onto the outdoor face of the specimen at the required rate and observing any water leakage”. Hence, it requires the air and water to be supplied simultaneously and for the testers to observe and document the rate of water leakage under the test conditions.
The test parameters typically require at least 20 gallons of water per hour (gal/hr) overall with between 4 – 10 gal/hr in any quarter section of the tested specimen, all at specified air pressure differentials. Given that this is a fairly stringent test, it is fair to say that metal roofing that holds up under these test conditions will likely perform well under most weather conditions when installed on a building. Typically, manufacturers have developed metal roofing products with seaming and connection methods that allow them to pass this test with virtually no observable water penetration.
To find out more about the tested results of metal roofing products you may be considering, contact your local MBCI representative or see the MBCI website and select the “testing” tab under a selected product.