Tag: metal roofing products
Against the Wind: MBCI’s Wind Rating Dominance
After a major, damaging storm, such as hurricanes and tornadoes, many things happen at once. Rescue efforts begin. Shelters open to house the displaced. Cleanup gets underway. But one thing that happens in the aftermath of such an event is a little harder to see – unless you’re looking for it.
The Building Material Post-Mortem
The Roofing Industry Committee on Weather Issues, Inc. (RICOWI) gathers experts and an army of volunteers to spend time on the ground at the disaster site, documenting damage. They take careful notes and photographs, looking closely at how different building methods, materials and ages withstood the storm. What they observe helps inform product development and ensure both installation standards and roofing products can stand up better to the next storm.
Unabbreviated
As the Metal Construction Association’s technical director Robert Zabcik said in a recent white paper, “Engineering professionals go through great efforts to make sure the public is protected.” All this research is integrated into regular updates to the tests, ratings and codes applied to building products across the country. These can become an alphanumerical soup, but here are the most prominent, along with differences between them:
Model Codes (Codes) provide a minimum baseline of performance needed to protect property and the public. These are the barebones building basics.
Underwriter’s Laboratories (UL) is a consortium of test labs and research companies which maintain test standards, as well as product listings which meet certain performance criteria. These are usually superior to those required by code.
Factory Mutual Insurance Company (FM Global) is comparable to UL but funded by a consortium of insurance underwriters.
Since the Miami-Dade area has suffered some of the worst hurricane damage, they have some of the most stringent codes and test protocols, so those are among many that MBCI uses to test our products. Jason Allen, MBCI research and development engineer, explained what some of these are and how they’re used. The UL 580 rating is based on tests for uplift resistance of roof assemblies. While materials can receive a class 30, 60 or 90 rating, MBCI uses class 90 as a standard. We also maintain class four impact ratings under UL 2218 for hail and projectiles, as well as the UL 790 Class A fire rating.
Any Way the Wind Blows
But these ratings and classifications get very complicated. You won’t find MBCI materials themselves listed as withstanding certain windspeeds or projectile damage. Allen explained, “It’s dependent on several things: building codes, roof pressures, eave and building height, facing attachments, roof slope and wind speed – just to name a few.” There are differences based on locality, storm threats and codes. It takes a qualified engineer to calculate all of it for an entire project. But that’s the only way to be sure of safety. “It’s going to cover all scenarios,” said Allen.
During a hurricane or tornado, wind is just part of the problem. “Performance during these events must consider both water tightness and wind applied at the same time,” said Zabcik. “Wind-driven rain can force water into places it would not normally go … This is yet another reason why details are so important and why manufacturers work so hard to ensure the systems they produce meet stringent standards for performance.”
In conditions like these, traditional building methods have a difficult time comparing to metal. They suffer from softer connections, more porous materials, and less stringent assembly designs. “Shingles last 15 to 20 years,” said Allen. “A metal roof can last 40 to 60 years.” Across the nation, wherever post-storm studies and material testing have occurred, metal stands out. In Florida Building Commission, FEMA and NIST studies, metal buildings performed exceptionally well.
Second Wind
Whether standing seam, insulated metal panels, exposed fastener or concealed fastener roof solutions are chosen, metal roofing’s strength and durability keeps out rainwater and withstands windspeeds that devastate other types of construction. Standing-seam roof systems and IMP façades remained intact during Hurricane Katrina even as winds hit 120 mph. “Industry experts have found that metal panel roofs can withstand wind gusts as strong as 140 mph or more due, in part, to their large interlocking panels,” said Zabcik. “Metal panel systems provide not only the weather resistive barrier,” he said, “but can also provide diaphragm stability to both the underlying framing and sometimes, the building as a whole, because they can transmit shear from one panel to the next.”
Riders on the Storm
What about hail raining down from the sky, windborne projectiles, lightning, and everything else that severe storms hurl at buildings? Though they may suffer some cosmetic damage, metal construction such as standing seam roofs and IMPs are often able to absorb impact, remain functional and keep their protective metal layers intact. That can make all the difference in a hurricane when the wind can blow away other roofs and dump untold gallons of stormwater and debris inside. Somewhat counterintuitively, metal buildings also perform very well during lightning strikes.
Batten Down the Hatches. Then Batten Them Again
Before you assume that selecting an engineer’s recommended, rated, and tested metal roof will be a sure-fire protection against all nature’s hazards, there’s one more thing to understand. All the ratings and tests mentioned here are performed with a specific assembly procedure. It is absolutely critical that the same procedure is followed – to a T – to ensure your building will enjoy the same protection its ratings guarantee. Allen recommends that you “look at the company you want and make sure they have statewide approvals,” and make sure your installer reads the manual, then re-reads it, then re-reads it a final time. It’s no exaggeration to say that lives are at stake.
Zabcik sums it up nicely: “With proper preparation, a solid knowledge of metal roofing options, an understanding of the latest standards and codes – not to mention a willingness to strictly adhere to tested quality control methods – today’s metal roofing is a strong choice for even the most vulnerable structure.”
To learn more about MBCI roofing solutions, to retrofit a current building or to get an engineer started on designing out your project in a storm-prone area, get in touch with an MBCI representative today.
Standard Testing For Metal Roofing – Part 2: Air and Water Resistance
In a prior post, we discussed the importance of independent (i.e. third party) standardized testing as a means of verifying the performance of metal roofing, and specifically looked at structural and wind uplift performance. In this post, we will similarly look at testing standards but focus on metal roofing tested for air leakage and water penetration.
Air Leakage and ASTM E1680
Keeping air from passing through a building system from the exterior to the interior (i.e. drafts) is a fundamental role of any building envelope system, including roofing. It is also important in controlling the flow of harmful airborne moisture into a roof assembly. Hence, testing a roofing panel for its ability to control air leakage is critical to the long-term success of the roofing system, and ultimately, the building.
ASTM E1680 “Standard Test Method for Rate of Air Leakage Through Exterior Metal Roof Panel Systems” is used to determine “the resistance of exterior metal roof panel systems to air infiltration resulting from either positive or negative air pressure differences”. It is a standard procedure for “determining air leakage characteristics under specified air pressure differences”. The test is applicable to the field portion of any roof area including panel side laps and structural connections but not at openings, the roof perimeter, or any other details. The test is also based on constant temperature and humidity conditions across the roofing specimen being tested to eliminate any variation due to those influences.
The standard test procedure consists of “sealing and fixing a test specimen into or against one face of an air chamber, supplying air to or exhausting air from the chamber at the rate required to maintain the specified test pressure difference across the specimen, and measuring the resultant air flow through the specimen”. Basically, the test is meant to reveal the ability of the selected roofing panel to resist the difference in air pressure between the two sides and thus demonstrate its air tightness.
The beauty of this standardized test is that different metal roofing products can be tested under the same conditions and compared. The standard calls for a pressure differential between the two sides of positive and negative 1.57 foot pounds of pressure per square foot of panel (75 paschals of pressure) and can be tested in the negative pressure mode alone if the roof slope is less than 30 degrees from horizontal.
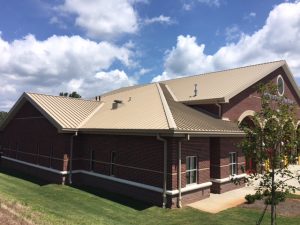
Water Penetration and ASTM E1646
In addition to air leakage, water leakage in roofing systems is obviously not desired. To test the performance of metal roofing products in this regard, ASTM E1646 titled “Standard Test Method for Water Penetration of Exterior Metal Roof Panel Systems by Uniform Static Air Pressure Difference” is the norm. This standard laboratory test is not based solely on free running water, but on water “applied to the outdoor face simultaneously with a static air pressure at the outdoor face higher than the pressure at the indoor face, that is, positive pressure”. This pressurized testing is intended to simulate wind-driven rain and flowing water that can build a head as it drains. The test measures the water-resisting properties of the roofing in the field of the roof panels including panel side laps and structural connections. Just like air testing, it does not include leakage at openings, perimeters, or other roofing detail areas.
The test method itself consists of “sealing and fixing the test specimen into or against one face of a test chamber, supplying air to or exhausting air from the chamber at the rate required to maintain the test pressure difference across the specimen, while spraying water onto the outdoor face of the specimen at the required rate and observing any water leakage”. Hence, it requires the air and water to be supplied simultaneously and for the testers to observe and document the rate of water leakage under the test conditions.
The test parameters typically require at least 20 gallons of water per hour (gal/hr) overall with between 4 – 10 gal/hr in any quarter section of the tested specimen, all at specified air pressure differentials. Given that this is a fairly stringent test, it is fair to say that metal roofing that holds up under these test conditions will likely perform well under most weather conditions when installed on a building. Typically, manufacturers have developed metal roofing products with seaming and connection methods that allow them to pass this test with virtually no observable water penetration.
To find out more about the tested results of metal roofing products you may be considering, contact your local MBCI representative or see the MBCI website and select the “testing” tab under a selected product.