Snow Removal
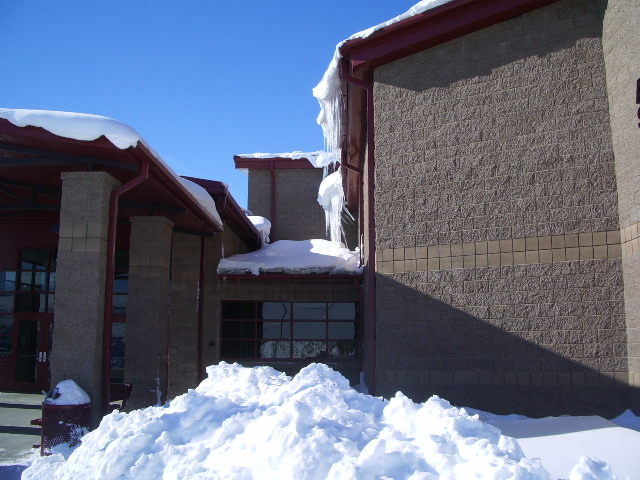
In our prior blog post, Benefits of Roofing Retrofits with Metal Roofing Systems, we looked at the benefits associated with retrofitting an existing building with a new metal roofing system. In this discussion, we will look at several ways to do it.
Buildings with flat roofs can be retrofitted with light-gauge steel framing systems to create a new sloped metal roof. Such systems can be installed directly over existing roofing membranes and structures, subject to appropriate structural engineering review. These systems typically use light-gauge (16 gauge to 12 gauge) steel framing installed directly above the existing roof to create a sloped plane. Regardless whether the existing roof structure is steel, wood or concrete, the new, lightweight framing system can be designed to disperse roof loading appropriately and connect securely.
The physical footprint of the existing roof, the type of framing system employed, and any special rooftop conditions will typically control the final geometry of the new sloped roof. A low-slope application (less than 2:12) can be selected based on economy and configured to discharge rainwater off of the roof. High-slope applications (greater than 2:12) are typically selected to improve and update the look of an existing building while improving long-term performance. Once the metal framing system is in place, then standing seam metal roof panels are commonly installed, creating a ventilated attic space in the process.
Low-slope metal roofing can be a great choice when a fairly utilitarian solution is needed for improving overall roofing performance. Exposed fastener systems can be used to allow direct installation of the new roofing panels over existing metal roofing or some other materials. Roofing panels specifically designed for retrofit applications typically have a rib spacing of 12″ on center with a rib height of just over an inch. The minimum slope for such a panel is 1/2:12. Any existing lap screws must be removed from the existing roof before the new panels are installed. The new retrofit panels are then attached with screws that fasten through the existing panel major ribs and into the existing purlins.
In some cases, an existing sloped roof may have another roofing material in place that is nearing the end of its service life. In that case, a new long-lasting, standing seam metal roofing system can be installed directly over the existing roof. Some systems will require a simple sub-framing system that allows the new roof to be installed directly over the existing. Retrofit roofing systems such as this can be UL-90 rated and FM Global rated. Other strategies exist to increase the energy efficiency of the building when adding new standing seam roofing, such as adding unfaced fiberglass insulated between the existing and the new roof and to vent the cavity between the old and new roofs by adding vent strips at the eaves, plus a vented ridge to allow air intake and exhaust. This method works well with roof slopes of 3:12 or greater.
Regardless of the specific system selected and designed, installing a retrofit metal roofing system allows the existing roof to remain in place, which saves on labor costs. It also minimizes the chance for water entry into the building during the roofing process and provides for a safer working environment. Existing rooftop equipment, vents, or light-transmitting panels can be accommodated by any of the systems described.
According to the Metal Construction Association (MCA), “retrofit metal roofing represents an economical and functional solution for building owners who want to beautify their existing structure or correct performance issues related to aging roofs and out-of-date materials. They have been employed in millions of square feet of existing commercial, industrial, retail and education facilities. The result is a new code-compliant metal roof that will last for 60-plus years, providing higher energy efficiency by reducing heat gain through the roof in summer months and reducing heat loss during winter months.”
To find out more about these retrofit systems, contact your local MBCI representative.