Tag: Aesthetics
Sealing the Deal: The Importance of Properly Sealing the Building Envelope Using IMPs and Single-Skin Panels
The primary purpose of a building’s envelope (roof and walls) is to protect the building’s interior spaces from the exterior environment and provide the desired exterior aesthetics. Whether choosing insulated metal panels (IMPs) for their superior performance or, instead, looking to the wide range of aesthetic choices available with single-skin panels—or some combination of the two—the common goal must always be to protect the building from the potential ravages of water, air, vapor, and thermal/heat. By ensuring proper installation of metal panels and, thereby, properly sealing the building envelope, problems can be mitigated, efficiencies maximized, and the integrity of the building protected.
Here, we’ll briefly consider the benefits of each panel, and some key considerations relative to their sealant needs and capabilities.
Insulated Metal Panels (IMPs)
IMPs are lightweight, composite exterior wall and roof panels that have metal skins and an insulating foam core. They have superior insulating properties, excellent spanning capabilities, and shorter installation time and cost savings due to the all-in-one insulation and cladding. In effect, IMPs serve as an all-in-one air and water barrier, and are an excellent option for retrofits and new construction. With their continuous insulation, roof and wall IMPs provide performance and durability, as well as many aesthetic benefits.
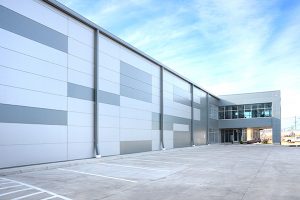
Generally speaking, because of the nature of the joinery, it is easier to get a good seal in place with IMPs given their relative simplicity (i.e., putting the two pieces together with the sealant). They require great attention, though, in terms of air and vapor sealing—aspects largely controlled by the installers on a given project. As an example, vapor sealing in cold climates or applications is critical to the overall soundness of a building. Consider the damage a building could incur if moisture seeps into a panel and becomes trapped; it if freezes, it could push panels out of alignment. This would result in not just an unattractive aesthetic, but a performance failure as well. In order to be effective, all sealant and caulking must be fully continuous.
Single-Skin Panels
Single-skin panels, alternatively, offer the advantage of an expansive array of colors, textures and profiles. They are also thought to have more “sophisticated” aesthetics than IMPs. Single-skin panels are available in both concealed fastener and exposed fastener varieties, and are part of an assembly. They can be used alone or in combination with IMPs, and as long as the needed insulation is incorporated, single-skin panels can meet technical and code requirements, depending on the application. Single-skin products offer a wide range of metal roof systems and wall systems as well.
Getting the proper seal on single-skin panels may require extra sealants or closures, and have more parts and pieces that have to come together to create the seal. However, when properly installed and sealed, they can provide excellent performance in their own right. Some key caveats include ensuring panel laps are properly sealed with either tape or gun butyl sealants, and carefully inspecting air and water barriers for proper installation as well as penetrations through the wall for sealing/fire caulking prior to panel.
In most cases, following the details for the most common conditions will give you a successful and high-performing outcome.
Regardless of the type of metal panel used, taking the time and effort to ensure the sealing and caulking details are properly handled, metal buildings can protect the built environment and provide long-lasting quality and performance.
Ventilated Metal Roofing Systems
Metal roofing is commonly installed on residential or light commercial buildings, where longevity and aesthetics are a priority. When those buildings are wood framed or use roof sheathing, the desired results can still be achieved, as long as some basic guidelines are followed. One of the most fundamental items to address is making sure that the roof system is properly ventilated in a manner that works with the rest of the building construction. Let’s take a look at the two most common means to achieve that.
Ventilated Attic:
Conventional residential roof construction typically involves a trussed or rafted roof system with insulation installed along the ceiling line and a ventilated attic above it. The premise here is that the ceiling is sealed tightly to prevent any conditioned air from entering the attic, but if it does, then any moisture in that air is ventilated out of the attic, preventing any build up and potential damage.
The most effective way to ventilate an attic is with continuous vents along the soffits and a corresponding continuous vent along the ridge. The International Residential Code (IRC) recognizes this approach and provides the formulas for determining the proper amount of net free vent area (NFVA) required for the total roof assembly. It then goes on to state that 50 percent should be split between the ridge vent and 50 percent along the total soffit area. Some building experts suggest, however, that 60 percent along the ridge and 40 percent along the soffits will provide a slight pressurization of the attic and help with the desired proper venting flow.
Either way, the overall intent is to create a situation where outdoor air is moving freely in through the soffit vents and up through the ridge vent. The continuously moving air then helps keep the roof sheathing, and the roof cooler than it would be when compared to sitting in the sun without the ventilation – on the order of at least 2-3 degrees Fahrenheit.
Ventilated Roofing:
Not every roof system is built with an attic and insulated ceilings. Sometimes, the roof deck defines the building enclosure either in the form of an upper floor ceiling or as a cathedral-style ceiling and roof system. In some of these cases, insulation may be installed between the roof framing which still requires ventilation between the roof sheathing and the insulation on the order of an inch minimum of air space (2 inches preferred), as in an attic.
In other cases, the insulation may be rigid foam that is installed above the roof deck or sheathing. Here, the insulation needs to be thick enough to keep the exposed ceiling warm and prevent any condensation inside the structure. The International Energy Conservation Code prescribes the minimum R-values of insulation based on climate zones, and typically, the required amounts for energy control also assure condensation control.
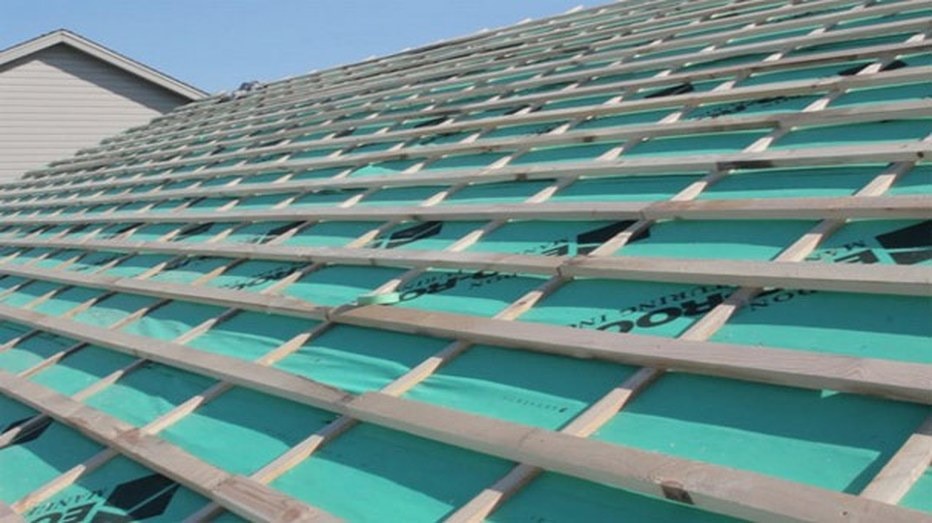
Nonetheless, if a layer of wood sheathing is placed directly on the insulation and then the metal roofing placed directly on top of that, the metal roofing will tend to get warmer in the sun than in a ventilated condition. Therefore, metal roofing manufacturers often recommend providing an air gap between the metal roofing and the sheathing. This is achieved with furring strips ran vertically to assure air flow, and then run horizontally to support the roof. The spacing and details of these supports should be determined by a structural engineer who can perform the needed analysis and calculations, taking into account the panel strength and imposed loads from snow, wind, etc.
Is this approach effective? A series of studies undertaken at Oak Ridge National Laboratory and sponsored by the Metal Construction Association has determined the answer is yes. These studies used a common asphalt-shingled roof without any ventilation above the sheathing as the control case. Then different versions of a metal roofing system with ventilation between the sheathing and the roofing were tested and compared to each other and the asphalt-shingled roof. The results found that “all test roofs were highly effective in reducing the heat flows through the roof and ceiling, and in reducing the diurnal attic temperature fluctuations.” (References below)
Clearly, paying attention to ventilating the roofing system, regardless of the type of construction, can make a difference in the overall performance of a roof. To find out more about ventilated roofing systems for a current or upcoming project, contact your local MBCI representative.
References:
Performance Evaluation of Advanced Retrofit Roof Technologies Using Field-Test Data – Phase Three Final Report
Authors: Kaushik Biswas, Phillip Childs, Jerald Atchley
Volume 1 Published: May, 2014 ORNL/TM-2014/141
Volume 2 Published: January 2015 ORNL/TM-2014/346
Prepared by OAK RIDGE NATIONAL LABORATORY
Oak Ridge, Tennessee 37831-6283
Managed by UT-BATTELLE, LLC for the U.S. DEPARTMENT OF ENERGY under contract DE-AC05-00OR227