Oil canning is a broad term in the world of metal panel products and is considered one of the most vexing issues facing metal panel installations. The Metal Construction Association (MCA) defines oil canning as a “visible waviness in the flat areas of metal roof and metal wall panels.” Oil canning, also known as elastic buckling or stress wrinkling, occurs in all types of metal panels. While it is a common concern, there are steps you can take to minimize the problem.
Here, we’ll focus specifically on oil canning/distortion with metal flush wall systems, which for MBCI products includes our FW Panels and Designer Series. The type of oil canning that occurs with flush wall systems is not caused by anything dealing with the product itself or with how it’s manufactured. Rather, it is a consequence of what installers are putting the metal panels on and how the installation is done.
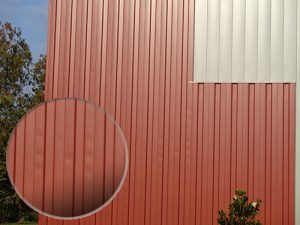
The simplest way to explain the phenomenon is that if the substructure is out of plane, i.e., not in alignment, stresses are put onto the panels that will create an appearance of oil canning. After all, as the old adage goes, you only get out what you put in. In the case of flush metal wall systems, the panels will look no better than what they are put on top of. If the substructure is wavy, out of plane, up or down, in or out, that condition will affect the panels’ performance and appearance.
Certain tolerances will have an effect on the panels’ appearance. With MBCI’s FW and Designer panels, tolerances would be 1/4 inch and 20 feet outward (away from two attachment points) and 0 inch and 20 feet inward. This means that if panels are forced into an inverted convex position, they will show stress rippling or oil canning more severely than when they’re stretched over a concave position, i.e., there can be some tolerance outward but zero inward.
With these types of panels, the biggest concerns with oil canning/distortion are aesthetics, but performance problems are also of concern, including possible engagement or sealing of the side joints.
Minimizing Oil Canning/Distortion of Panels
Prior to installation, installers should be checking the substructure with string lines or lasers and correcting or shimming any areas that are out of plane, especially since oftentimes substructures, such as stud walls or structural walls that the metal panels are attached to, are installed by other trades. Metal panel installers need to scrutinize each aspect for alignment and then either correct or shim to bring it within tolerance and within plane.
As is true with any metal panel product, for best results, proper handling and installation go a long way towards preventing the problem of oil canning in the field.
To find out more on how to minimize oil canning on your MBCI metal wall panels, contact your local MBCI representative, and sign up for our newsletter to subscribe to our blog.