Metal panel installers have a tough job—not only navigating the details of the task at hand but also being confident enough to know when to seek the manufacturer’s guidance. Part of overseeing a successful project is for the installer to know when something is out of his or her comfort zone, beyond their expertise, or just doesn’t look or feel right. And when that’s the case, it’s imperative to call on the manufacturer for input before it’s too late.
Technical support, such as MBCI’s Ask the Technical Expert, can be most useful for answering upfront general product questions. Once the project has started or material is on the jobsite, it’s generally preferable for the installer to go through their sales person or field service/customer service representative rather than sending a question via a website.
When to Seek Assistance from the Manufacturer
First things first: The installer should study the installation manual and construction drawings. If, after that, he or she is experiencing a problem—for instance, the panel doesn’t look right, it’s not engaging properly, it’s not meeting the tolerances stated in the manual, the fasteners that are called out in the drawings are not working or are even missing—then contacting the manufacturer should be the next step. That one simple call can save a lot of time in potential headaches.
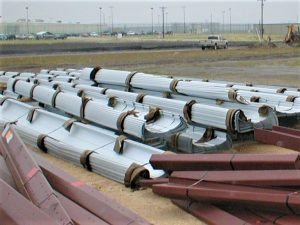
While it’s not the manufacturer’s direct responsibility to make sure the installer is doing the job on site per the drawing details, a reputable manufacturer can at least provide recommendations when asked how to possibly alleviate or mitigate any number of potential pitfalls, or share common oversights that other installers have made—and how to avoid those same mistakes.
Top Circumstances
Here are two of the top circumstances under which MBCI recommends immediately reaching out to the manufacturer:
- Damage to the physical panel itself. If a customer receives materials and there’s suspected or noticeable damage to it, he or she may or may not know what impact that damage could initially have on the system. Notify the manufacturer immediately to assess if it’s a minor issue or if the panels should not be installed because it will be detrimental to the system. No one wants to have to reorder or wait for new materials, but it’s worse to wait until after installation when the impact of removing/replacing is significantly more costly and time-consuming.
- Fasteners. Contact the manufacturer if the substrate on site changes in any form from the project details, there is any difficulty with the screws themselves engaging, or any problems with the fastener type. When installing fasteners, make sure to use the ones per the installation details. The manufacturer can assist in verifying the correct fastener is being used in the correct location per the details and per the substrate on site. There could be situations where the installer is not accurately reading the drawing or has substituted an alternative screw not supplied by the manufacturer. Don’t assume. Instead, call.
There are, of course, other scenarios when a call to the manufacturer will save time, money and aggravation for all parties involved in an installation, including alignment and substrate issues, the addition of accessories, and problems with panel engagement. In Part 2 of this topic, we will go into more detail on these additional circumstances.
For more information on metal roof and wall products and training, MBCI offers courses through its Metal Institute. These courses are available for general training purposes or for those seeking installer certification.